Laser Processing of High-Density Structures over Large Areas
High Precision – High Throughput – Simultaneous 2D Processing
The processing of high-density structures across large areas, such as laser drilling or laser marking of printed circuit boards (PCBs), requires solutions that provide high precision and high throughput. This application-specific technology demonstrator shows the combination of multi-axis positioning systems and a highly dynamic galvanometer scanner that fulfills industrial production needs.
SCANLAB GmbH produces galvanometer scanners, with certain models being enhanced to synchronously control a 2D scan head and two mechanical axes, for example, an XY stage with two servo axes. PI’s ACS motion controller platform enables this feature, known as XL SCAN, and the solution provides an almost limitless working area when used with PI’s motorized positioner portfolio.
XL SCAN allows continuous operation across large areas, therefore avoiding idle time and eliminating stitching errors. The ability to extend the field of view (FOV) by the stages’ travel ranges have the advantage that the optics can be fixed and maintained in terms of accuracy, spot size, and performance.
System integrators are responsible for integrating the components, configuring the control software, calibrating the system, and addressing any issues that arise during the integration process. Their expertise is vital for the XL SCAN system to achieve its desired performance and functionality.
Features of the XL SCAN Automation Solution
- Extended process area
- Increased throughput
- Increased processing accuracy to the micron level
- No stitching errors
- Smooth processing with high dynamics and no stage vibrations
- Automatic laser control, e.g. Spot Distance Control (SDC)
- Multiple scan heads and workpiece motion systems capability
Laser Beam Steering
- Fast and precise excelliSCAN scan system from SCANLAB with an XY galvanometer scanner for beam control
>> SCANLAB excelliSCAN scan-head
Workpiece Positioning
- XY linear motor stages or planar scanners for high geometric characteristics and high velocity
>> V-731 High-Precision XY Linear Motor Stage - Optional granite support for high accuracy and stability
- Alternative gantry arrangement with stationary workpiece and moving scan head
Automation Control
- Motion control solution jointly-developed by SCANLAB and ACS Motion Control which integrates a digital scanner technology using EtherCAT®-based industrial networking
>> ACS Motion Controllers
>> ACS Drive Modules - Synchronization of galvo and stage motion controller is achieved through unique SL2-100 to EtherCAT® interface
>> ACS SLEC Laser Control - System control software which integrates the control of motion, scanner and laser at the process level
>> ACS SPiiPlusSPC
>> SCANLAB syncAXIS Software
Schematic Layout of a Standard XL SCAN Setup
The XL SCAN method provides simultaneous and coordinated control of the workpiece motion system, the scanner, and the laser modulation. The control software of XL SCAN automatically splits the desired pattern trajectory into a path for the scanner, a path for the XY stages and the control for the laser spot. The scanner receives high-frequency motion signals for short distances. The positioning stages with long travel ranges get the low frequencies and they enlarge the working area. Both motions are performed simultaneously.
Extended Process Area and Increased Throughput
Conventional methods for processing large fields use a “step and scan” approach, which divides the machining area into individual sections. This piecewise processing is slower and generates stitching errors at boundaries. XL SCAN provides a working area enlarged by the long travel ranges of the PI motion systems and allows fast continuous motion across the extended field without stitching errors.
Increased Accuracy
The XL SCAN method takes advantage of the zero tracking error of the excelliSCAN scan head. In combination with the XL SCAN trajectory planning, the advanced jerk-limited motion control and PI’s motion systems with corresponding dynamics, straightness, flatness, and precision, high process accuracies can be achieved. The process accuracy of the scan head is proportional to the distance of the processing point from the center of the scanning field. XL SCAN enables the scan head to work closest to the center of its FOV which in turn is directly related to accuracy.
Simultaneous Control of Spot Distance and Pulse Energy
Both pulse energy and the spot distance can be controlled simultaneously. Spot distance control (SDC) outputs to the laser either a single pulse or a series of pulses. SDC allows a constant energy deposition per unit length. Triggering a laser pulse is based on the travel distance and is independent of the movement speed and the pattern of the laser path. Curved and straight sections can be processed at there respective maximum speed while maintaining accuracy and maximum throughput.
Ramping of Laser Power and Deflection-Angle-Dependent Control
For certain processing operations, a specific laser power along a path may need to be defined. XL SCAN allows the user to define the power level specifically for different parts of the path. In addition, laser spot size depends on the deflection angle of the scan head. The deflection-angle-dependent laser control of XL SCAN keeps energy density constant and minimizes spot size variations along the laser path.
Downloads
Automation Platforms for Laser Material Processing
Precision – Throughput – Synchronized Motion
Do you have questions about our solutions? Our specialists are happy to help you!
Contattaci oggi stesso!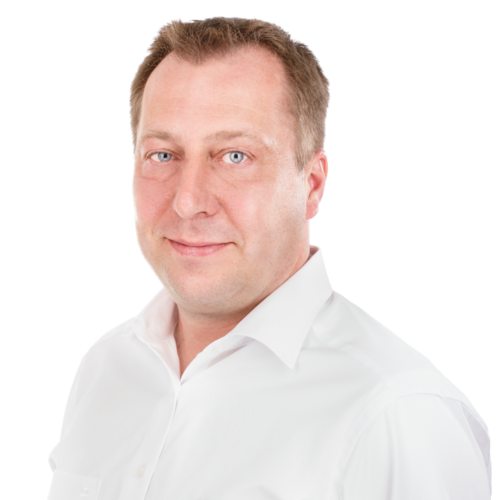