Characterization of Light Emitting Devices
Fast Active Alignment
The classic application focus of Optical Coherence Tomography (OCT) is the medical field of ophthalmology. However, today, OCT also gets considered for applications in industrial environments such as printed circuit board (PCB) layer diagnostics, and material surface analysis. Modern OCT solutions demand light sources with a high spectral bandwidth and a long coherence length. Super luminescent emitting diodes (SLED) and swept laser sources (SLS) are both light sources that need to fulfill increasingly demanding customer requirements. For this reason, SLED and SLS are becoming more expensive, meaning that a quality check is economically unavoidable before completing the next step: Packaging the SLED and SLS in butterfly packaging.
Fast and synchronized testing on-the-fly can be realized with PI’s Fast Multi-Channel Photonics Alignment (FMPA) systems. Automated area scans allow fast and reliable high-resolution emission profile analysis. Additionally, the intelligent gradient search algorithm can track the position of the optimum of any figure of merit e.g. light intensity for hours. These two algorithms are the core of the FMPA solution that run on many PI controllers. The variety of positioning systems on all length scales allows PI to find the perfect solution for light source quality control.
Key Features of the Alignment Solution
XYZ/ θX θY θZ – Automatic Submicron Alignment of the Optical Fiber
- Parallel-kinematic hexapod for fast alignment over long travel ranges in six degrees of freedom
- High stiffness of the mechanical design provides high dynamics and short settling times
- Freely definable center of rotation adresses geometrical offsets
- Position sensors ensure high accuracy and operational reliability
- Compact design for space saving integration
>> H-811.I2 6-Axis Miniature Hexapod
>> F-712 Single-Sided Fiber Alignment System
XYZ Axis – Automatic Nanometer Alignment of the Optical Fiber
- Parallel-kinematic piezo system for fast scanning motion
- High stiffness of the mechanical design provide fast scanning motion and tracking
- Zero-play flexure guides for high guiding accuracy, without any wear or particle generation
- Integrated sensors offer excellent linearity of motion, long-term stability, and scanning frequency of up to 100 Hz
- All-ceramic insulated piezo actuators for outstanding lifetime
>> P-616 NanoCube® Nanopositioner
>> F-712 Single-Sided Fiber Alignment System
θZ Axis – Reliable and Scalable Placing of the Optical Components
- Highly accurate and repeatable 360° rotation without backlash
- High velocities and accelerations due to magnetic direct drives
- Ironless linear motors provide smooth and precise operation without cogging
- Low profile design for space saving integration
>> V-610 Compact PIMag® Rotation Stage
User-Friendly and Flexible Automation Control
- EtherCAT® interfaces enables fast integration into high-throughput industrial systems
- High-performance industrial controllers automate built-in scans and optimizations with millisecond responsiveness
- Proprietary firmware enables fast alignment of fibers based on fast area scanning algorithm for first light detection and gradient search for peak coupling
- Software support for fast application development on all common operating systems such as Windows, Linux, and MacOS as well as many common programming languages including MATLAB , Python, C# and NI LabVIEW
- Quick start-up and ease of use with PI MicroMove software
>> C-887 Hexapod Motion Controller
>> E-712 Digital Piezo Controller
Do you have questions about our solutions? Our specialists are happy to help you!
Contattaci oggi stesso!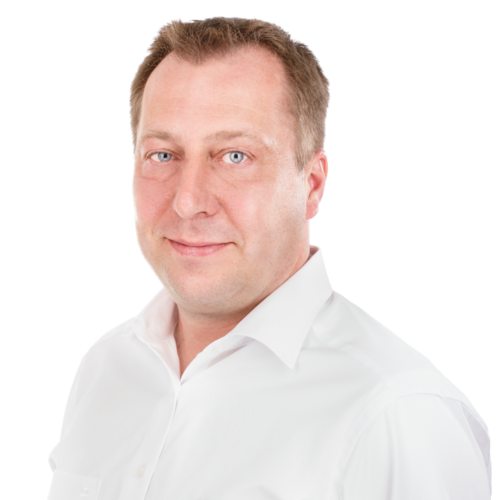