Wafer Inspection & Metrology
Highly Dynamic and Precise Motion System for Wafer Positioning
Efficient wafer inspection and metrology are essential for ensuring a stable, high-performance semiconductor manufacturing process. With up to 800 complex production steps, semiconductor fabrication demands precise inspection and metrology at every critical stage to guarantee the highest levels of quality and yield.
PI’s advanced motion and positioning solutions are at the forefront of supporting critical applications like overlay metrology, thin film metrology, edge placement error (EPE) metrology, and automated optical inspection (AOI). By integrating wafer scanning and high-speed measurement capabilities with dynamic positioning and ultra-precise Z-focus adjustments, PI enables advanced process control that helps manufacturers catch defects at the earliest possible stage. This technology is being designed with various configurations to address specific application requirements, ensuring flexibility and adaptability across different semiconductor processes. With cutting-edge motion control and sophisticated algorithms, these solutions minimize yield losses and drive down production costs.
XY Axis - Precision Scanning and Step-and-Settle Motion
- Granite base for high stiffness and increased flatness and straightness
- Ironless direct drive linear motors for high, cog-free scanning speed and fast step-and-settle motion
- High-resolution encoders for fast startup, reliability, and safety
- Integrated cable management for reduced motion drag and long lifetime
- Optional granite-based planar scanner with air bearings and yaw control for 24/7 high duty cycle operations with minimal runout errors and nanometer straightness and flatness
>> Direct Drive Linear Motor Stages
>> Planar Scanner with Air Bearing
θZ Z Tip/Tilt Axis - Wafer Positioning
- Multi-axis, hybrid piezo motor technology providing compensation of wafer misalignment and high bandwidth dynamic focus tracking
- Energy-free position lock eliminating the need for additional cooling or balancing
- Stable positioning of the wafer during inspection with position stability of < 10 nm
- Move and settle times down to < 10 ms
- Integrated DC motor for wafer lift with bidirectional repeatability < 1 µm
>> Highly Dynamic and Precise Piezo Wafer Positioning Solutions
Flexible and Easy Automation Control
- EtherCAT® controller for open network connectivity
- Advanced algorithms provide fast step-and-settle, high in-position stability, and exceptional constant scanning velocity
- Advanced ACS control features, optionally available with additional algorithms (trajectory optimization, image recognition, „first-fault-finding“, motion error, input shaping, and EtherCAT protocol)
- Combined ACS and piezo controller with bi-directional communication for real-time motion control
- Autofocus capabilities of the controller for dynamic focus adjustment
- Look-ahead capability adjusts velocity to maintain accuracy
>> Motion Controllers
θZ Axis - Fine Rotary Indexing and Alignment of Wafer or Substrate
- Highly accurate and repeatable 360° rotation without backlash
- High velocities and accelerations due to magnetic direct drives
- Direct-drive, slotless, brushless torque motor offers very low cogging torques and enables smooth speed and low error motions
- Ultra-precise air bearings developed and manufactured in house
- Next level performance to further optimize asynchronous performance specifications
>> Technology of Direct Drive Torque Motors
Z Axis - Precision Wafer Alignment
- Low profile, high load, compact superior design
- Direct drive voice coil technology provides zero cogging, smooth motion with nanometer step size and response
- High-resolution encoder for nanometer positioning of the motion platform
- High-precision anti-creep crossed-roller bearings
- Pneumatic counter balance prevents motor heating and avoids collisions
- Economically priced with fast delivery
>> Technology of Direct Drive Motors
XY Axis - Precision Step-and-Settle Motion
- High-dynamics, coupled ironless linear motors on base axes for powerful, fast and precise motion
- Dual encoder system ensures motor and yaw alignment, while providing high resolution and accuracy
- Multiple bearing stiff platform with low profile reduces abbe offsets and offers increased flatness and straightness
- Design allows high flexibility and customization
- Optimized integrated cable management reduces motion drag and prolongs lifetime
- Granite base ensures highest performance of the motion system
- Optional active isolation
>> Direct Drive Linear Motor Stages
Flexible and Easy Automation Control
- EtherCAT® controller for open network connectivity
- Advanced algorithms provide fast step-and-settle, high in-position stability, and exceptional constant scanning velocity
>> ServoBoost™ - Autofocus capabilities of the controller for dynamic focus adjustment
- Look-ahead capability adjusts velocity to maintain accuracy
>> Motion Controllers
Do you have questions about our solutions? Our specialists are happy to help you!
Contattaci oggi stesso!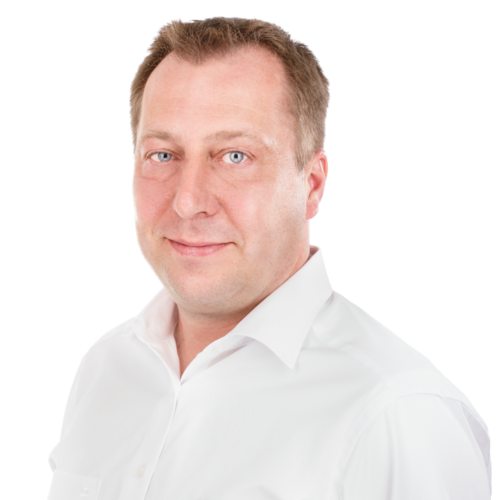